Monday, May 25, 2009
India to Buy 200 Aircraft Instead of 126
Friday, May 15, 2009
India to Develope More UCAV Technologies
Tuesday, May 12, 2009
Aerodynamics
The main job a of a fighter has always been to catch and destroy the enemy aircrafts. To achieve this they need speed and a good rate of climb. This is hopefully enough to take the opponent by surprise. Maneuverability is also a key defensive attribute which enables the fighter to get away from the opponents envelope.The two main types of maneuverability are to transient and turn. Transient are the ability to change the flight mode to another; pitch, roll and yaw.
The roll is caused by ailerons on the wings, or fins past by spoilers dumped loft on one side. Turning ability is determined by the amount of loft a wing can produce. The fighter with the lowest wing loading will outrun it’s opponent. A fighter like the Indian SU 30MKI with extreme maneuverability can just get a pilot inside the extremely agile F-16 dizzy and take it down.
A different way to look at fighter performance is to look at the position and kinetic energy. Position-altitude which can be converted into speed by diving and kinetic energy-which is the combination of it’s mass and velocity.
Conventional fighter maneuverability depends on the lift created by its wings. So wing design therefore is very important. A long wingspan maximizes the lift but reduces the rate of roll. To solve this problems variable sweep wings with wider aspect ratio were created.
Modern Fighter Planes
Modern fighter jets have awesome capabilities. Most can achieve speeds that are faster than sound and touch the edge of the sky. It does not have to see its enemy; It can sense and destroy it far beyond visual range. It can perform unbelievable gyrations.
The fighters are designed to meet two factors: its enemies and the medium which it operates in. The enemies can come in many forms. It can com from the air, land and water. Like the threats, it’s medium can also differentiate due to its properties.
Air defense is not simply about dogfighting with the fighters they have to worry about Surface to air missiles (SAMS), anti-aircraft artillery (AAA) and ground based radar. The medium in which the fighters operate is the air. Like its threats air is extremely variable; at see level the air is denser so the jet engine absorbs plenty of oxygen which can result in maximum thrust but the bad news is that dense air means greater drag.
Monday, May 11, 2009
F-16 Performs First Robot Landing
Lockheed Martin and the U.S. Air Force Test Pilot School at Edwards Air Force Base, Calif., report successfully demonstrating an autonomous landing of the F-16 Fighting Falcon, marking the first time an F-16 has landed entirely under computer control.
The successful Autoland demonstration lays the foundation for consistent, repeatable and controlled automatic landings of the F-16 in various wind conditions and airfield situations. This Lockheed Martin-developed technology has broad applications for both manned and unmanned aircraft.
“The demonstration of an autonomous landing of an F-16 is evidence that Lockheed Martin is prepared to successfully implement autonomous control of Unmanned Combat Air Vehicle (UCAV)-type aircraft,” said Frank Cappuccio, Lockheed Martin’s executive vice president and general manager of Advanced Development Programs and Strategic Planning. “Such technology, in concert with the skill and experience of today’s warfighter, presents a formidable force against existing foes and provides a basis for further developing manned and unmanned vehicles that can meet the challenges facing the warfighters of tomorrow,” he said.
The Autoland sequence is initiated during flight by an on-board safety pilot. Once the pilot moves to “hands-off” the aircraft controls, the F-16 is controlled by an onboard computer and guided through several phases of the landing sequence, culminating in a final approach to the runway touchdown point. The computer uses Lockheed Martin-developed algorithms to control the F-16’s attitude, glide slope, airspeed, and descent rate via throttle and flight control inputs until the aircraft comes to a stop on the runway.
The USAF Test Pilot School provided full flight test resources for the demonstration, including the VISTA/F-16 (Variable Stability In-flight Simulator Test Aircraft), Calspan Corporation flight test safety pilots (under contract to the Test Pilot School), and testbed support and facilities. Lockheed Martin Aeronautics and the USAF Test Pilot School performed all activities in full partnership, from initial planning through implementation and test execution.
Sunday, May 10, 2009
Raytheon To Transfer AESA Tech To India
American space and airborne systems company, Raytheon, has said that the Indian Air Force (IAF) will get access to cutting-edge radar technology in the form of the AESA radar, up to the level permitted by the US government, should it decide to opt for the Boeing F/A-18E/F Super Hornet under its global tender for 126 medium-range multi-role combat aircraft (MMRCA) tender.
“We are willing to support Active Electronically Scanned Array (AESA) radar technology transfer up to the level the US government allows us,” said Dave Goold from Raytheon’s F-18 business development, Tactical Airborne Systems.
“The technology transfer, though likely to be limited, would meet the requirements of the IAF. Our proposal will be compliant with the request for proposal (RFP) issued by the IAF for the 126 combat aircraft,” he said.
The AESA radar lends an edge to the F/A-18E/F Super Hornet by increasing its air-to-air detection and tracking range, apart from enhancing its air-to-ground targeting capabilities. So far, the US government has allowed transfer of the cutting-edge AESA radar technology only to Australia.
Raytheon is a systems supplier for the Super Hornet Boeing’s F-18 multi-role ground fighter which is one of the six contenders for the IAF’s MMRCA contract along with Lockheed’s F-16, Russia’s MiG-35, the French Dassault’s Rafale, the Swedish Saab Gripen JAS-39 and the Eurofighter Typhoon.
Saturday, May 9, 2009
Boeing Recognized as NASA’s Large Business Contractor of the Year

"Boeing’s partnership with NASA at the space center ensures mission success in support of America’s space programs," said Mark Jager, Boeing CAPPS program manager. "This partnership is strengthened by the contributions of our small-business teammates and our commitment to the local community."
As the prime contractor for NASA’s CAPPS contract, Boeing provides payload processing services for the International Space Station, space shuttle and expendable launch vehicles. Boeing employees and teammates have successfully processed every major payload flown on the space shuttle — work that began with Columbia’s first flight in April 1981.
Source: Boeing Integrated Defense Systems
Friday, May 8, 2009
Geocaching Devices
Device Feature Considerations for Geocaching
- Basemap. This is highly recommended. The additional cost is marginal, and the increase in the equipment’s usefulness is substantial. Driving directions to the area near a cache can be incredibly useful, so consider this feature in a higher end device.
- Channels. Most GPS units today now have 12 parallel channels. Channels help to acquire GPS satellite signals faster and more accurately. If you are looking at older GPS devices, consider models built after 1997. Older, single-channel receivers are much slower and may not be as accurate.
- External antenna jack. With new GPS devices this has become less important since the newer chips are sensitive enough to acquire signal inside a vehicle. However, it is not always possible to obtain good satellite coverage through a front windshield; this is when an external antenna can help. Even backpackers will benefit from the ability to safely store the receiver inside a pack with an antenna attached to backpack shoulder straps. It can also help outdoor use in places, like heavy tree cover, where signals are weak.
- Interface jack. If you are using the receiver with a computer, be sure that it includes an interface cable so you can quickly load maps and waypoints onto your device. Newer GPS units often support USB while older devices generally have serial attachments. If you purchase an older GPS device and have a newer computer, you may need to purchase a USB to serial port adapter as well. If you own a Mac, you should check to ensure that it supports the Mac operating system.
- Memory. This is used to load detailed topographic maps, street-level maps, or additional waypoints into the receiver. Detailed maps can use a great deal of memory on your device. Consider internal storage capacity. Higher end devices also usually accept a memory card for additional storage.
- Power source. It is preferable to have a device that can support external power, like a cigarette lighter power cable. Due to the power requirements the device should support standard batteries (AA or AAA) for easy replacement on the trail. Lithium batteries are recommended for newer GPS models to ensure a longer battery life, and power geocachers should consider rechargeable batteries.
- Rocker keypad or touchscreen. Using a receiver without a rocker keypad is like using a computer without a mouse. Some newer GPS units have touchscreens which helps immensely when navigating using the maps.
- Screen size. For visual ease of operation, use a device with the largest screen that can be realistically carried. Screen size is measured diagonally. Color is great and helps define map features and a backlight is important, although both features burn additional battery power. A screen protector is important in preventing scratches out on the trail.
- Waterproof. Sooner or later your device will get submerged. Get a device that is at least water-resistant, although an IPX7 designation is preferred. An IPX7 designation means the GPS case can withstand accidental immersion in one meter of water for up to 30 minutes. Plastic bags and boxes are also recommended for added protection.
- Geocaching Features. An increasing number of higher end GPS devices now have functionality specifically created for geocaching that can store all the information from Pocket Queries. Some will also store field notes to help you log your caches after a hunt.
Thursday, May 7, 2009
F-35 Lightning II Avionics Tested
Lockheed Martin’s Cooperative Avionics Test Bed, or “CATBird,” has begun in-flight integration and verification of the F-35 Lightning II mission systems suite, launching another stage of risk reduction for the world’s newest fighter.
The CATBird, a highly modified 737 airliner, will test the avionics suite thoroughly for several months before the complete system begins flying in an F-35 aircraft. The entire F-35 avionics system is slated for airborne testing in the CATBird in 2009.
“The F-35 mission systems suite is the most sophisticated and powerful avionics package of any fighter in the world,” said Dan Crowley, Lockheed Martin executive vice president and F-35 program general manager. “The CATBird is a shared industry and government investment that continues our risk-reduction work as we prove that the F-35’s advanced avionics work as advertised, three years before the first F-35 goes operational. This is the start of what will no doubt be an exciting period of validation and confidence building regarding the capabilities of this 5th generation, multi-role, multi-service aircraft.”
The F-35’s avionics include on-board sensors that will enable pilots to strike fixed or moving ground targets in high-threat environments, day or night, in any weather, while simultaneously targeting and eliminating advanced airborne threats.
The CATBird’s 40th flight, on Tuesday, Nov. 25, was its first configured as a complete classified mission systems laboratory. All test objectives were met in the 2.4 hour sortie.
“We were able to transmit using the radar for 23 minutes and selected six different TACAN (tactical control and navigation) stations, with data displayed on the F-35 cockpit that resides in the CATBird,” said Eric Branyan, Lockheed Martin vice president of F-35 Air System Development. “The results matched our predictions.”
The first Lightning II aircraft to fly with the full avionics package will be a short takeoff/vertical landing F-35B, called BF-4. All previous F-35 test aircraft are “flight sciences” aircraft, designed to validate the fighter’s aerodynamic performance. BF-4 is the first F-35 “mission systems” aircraft and is scheduled to make its first flight in mid-2009.
The F-35 is a supersonic, multi-role, 5th generation stealth fighter. Three F-35 variants derived from a common design, developed together and using the same sustainment infrastructure worldwide will replace at least 13 types of aircraft for 11 nations initially, making the Lightning II the most cost-effective fighter program in history.
Lockheed Martin is developing the F-35 with its principal industrial partners, Northrop Grumman and BAE Systems. Two separate, interchangeable F-35 engines are under development: the Pratt & Whitney F135 and the GE Rolls-Royce Fighter Engine Team F136.
Wednesday, May 6, 2009
Honeywell Provides Safety Avionics and Mechanical Products for Wizz Air to Reduce Costs and Improve Fuel Efficiency
Honeywell will provide a suite of its safety and navigational avionics products and the 131-9A Auxiliary Power Unit (APU) for installation on 70 new Airbus A320 family aircraft to Wizz Air Hungary Ltd. The airline also finalized a long-term service agreement on the Honeywell APU.
The advanced avionics suite includes the IntuVue™ radar system, Honeywell’s 3-D weather radar that allows pilots to better see and avoid weather, wind shear and turbulence, ensuring a safer and more comfortable ride for passengers.
Wizz Air selected Honeywell’s 131-9A APU, which provides class-leading fuel efficiency and low cost of ownership. Honeywell continues to pursue energy efficiency innovations, including the recent implementation of a fuel burn de-rate upgrade that reduces APU fuel consumption by 5 percent.
“This is a terrific example of an airline incorporating all of the energy efficiency savings Honeywell can provide, from making an individual aircraft more efficient with fuel saving APUs to helping the aircraft operate more efficiently in the air traffic system,” said T.K. Kallenbach, Honeywell Aerospace Vice President of Marketing and Product Management.
“Honeywell was able to offer us the right combination of avionics products to improve the quality of operations while reducing operating costs,” said Marc Weber, Head of Technical Services at Wizz Air. “At the same time the Honeywell service agreement for the APUs provides us with a long term, high quality maintenance solution.”
Tuesday, May 5, 2009
Integrated Modular Avionics
IMA modularity simplifies the development process of avionics software :
* As the structure of the modules network is unified, it is mandatory to use a common API to access the hardware and network resources, thus simplifying the hardware and software integration.
* IMA concept also allows the Application developers to focus on the Application layer, reducing the risk of defaults in the lower-level software layers.
* As modules often share an extensive part of their hardware and lower-level software architecture, maintenance of the modules is easier than with previous specific architectures.
* Applications can be reconfigured on spare modules if the module that support them is detected faulty during operations, increasing the overall disponibility of the avionics functions.
Communication between the modules can use an internal high speed Computer bus, or can share an external network, as of ARINC 429 or AFDX.
It must be noted that there is no overall hardware or software standard that defines all the mandatory components used in an IMA architecture. However, parts of the API involved in an IMA network has been standardized, such as:
* ARINC 653 for the software avionics partitioning constraints to the underlying Real-time operating system (RTOS), and the associated API
* AFDX for the data network bus.
Examples of IMA architecture
Examples of aircraft avionics that uses IMA architecture :
* Rafale : Thales IMA architecture is called MDPU (Modular Data Processing Unit) [4][5]
* F-22 Raptor
* Airbus A380 [2][6]
* Boeing 787 : GE Aviation Systems (formerly Smiths Aerospace) IMA architecture is called Common Core System [2][7]
* Dassault Falcon 900, Falcon 2000, and Falcon 7X : Honeywell’s IMA architecture is called MAU (Modular Avionics Units), and the overall platform is called EASy[8]
* Sukhoi Superjet 100
* ATR 42
* ATR 72
* Airbus A350
Avionics software
Avionics software is embedded software with legally-mandated safety and reliability concerns used in avionics. The main difference between avionic software and conventional embedded software is that the development process is required by law and is optimized for safety.
Interestingly, some claim that the process described below is only slightly slower and more costly (perhaps 15 percent) than the normal ad-hoc processes used for commercial software. Since most software fails because of mistakes, eliminating the mistakes at the earliest possible step is also a relatively inexpensive, reliable way to produce software. In some projects, however, mistakes in the specifications may not be detected until deployment. At that point, they can be very expensive to fix.
The basic idea of any software development model is that each step of the design process has outputs called “deliverables.” If the deliverables are tested for correctness and fixed, then normal human mistakes can’t easily grow into dangerous or expensive problems. Most manufacturers follow the waterfall model to coordinate the design product, but almost all explicitly permit earlier work to be revised. The result is more often closer to a spiral model.
For an overview of embedded software see embedded system and software development models. The rest of this article assumes familiarity with that information, and discusses differences from commercial embedded systems and commercial development models.
Development process
The main difference between avionics software and other embedded systems is that the actual standards are often far more detailed and rigorous than commercial standards, usually described by documents with hundreds of pages.
Since the process is legally required, most processes have documents or software to trace requirements from numbered paragraphs in the specifications and designs to exact pieces of code, with exact tests for each, and a box on the final certification checklist. This is specifically to prove conformance to the legally mandated standard.
Deviations from a specific project to the processes described here can occur due to usage of alternative methods or low safety level requirements.
Almost all software development standards describe how to perform and improve specifications, designs, coding, and testing (See software development model). However avionics software development standards add some steps to the development for safety and certification:
Human interfaces
Projects with substantial human interfaces are usually prototyped or simulated. The video tape are usually retained, but the prototype retired immediately after testing, because otherwise senior management and customers can believe the system is complete. A major goal is to find human-interface issues that can affect safety and usability
Hazard analysis
Safety-critical avionics usually have a hazard analysis. Very early in the project, there’s usually at least some vague idea of the main parts of the project. An engineer then takes each block of a block diagram and considers the things that could go wrong with that block. Then the severity and probability of the hazards are estimated. The problems then become requirements that feed into the design’s specifications.
Projects involving military cryptographic security usually include a security analysis, using methods very like the hazard analysis.
Maintenance manual
As soon as the engineering specification is complete, writing the maintenance manual can start. A maintenance manual is essential to repairs, and of course, if the system can’t be fixed, it won’t be safe.
There are several levels to most standards. A low-safety product such as an in-flight entertainment unit (a flying TV) may escape with a schematic and procedures for installation and adjustment. A navigation system, autopilot or engine may have thousands of pages of procedures, inspections and rigging instructions. Documents are now (2003) routinely delivered on CD-ROM, in standard formats that include text and pictures.
One of the odder documentation requirements is that most commercial contracts require an assurance that system documentation will be available indefinitely. The normal commercial method of providing this assurance is to form and fund a small foundation or trust. The trust then maintains a mailbox and deposits copies (usually in ultrafiche) in a secure location, such as rented space in a university’s library (managed as a special collection), or (more rarely now) buried in a cave or a desert location.
Design and specification documents
These are usually much like those in other software development models. A crucial difference is that requirements are usually traced as described above. In large projects, requirements-traceability is such a large expensive task that it pays for large expensive computer programs to manage it.
Code production and review
The code is written, then usually reviewed by a programmer (or group of programmers) that didn’t write it originally (another legal requirement). Special organizations also usually conduct code reviews with a checklist of possible mistakes. When a new type of mistake is found it’s added to the checklist, and fixed throughout the code.
The code is also often examined by special programs that analyze correctness (Static code analysis), such as SPARK examiner for the SPARK (a subset of the Ada programming language) or lint for the C-family of programming languages (primarily C, though). The compilers or special checking programs like “lint” check to see if types of data are compatible with the operations on them, also such tools are regularly used to enforce strict usage of valid programming language subsets and programming styles. Another set of programs measure software metrics, to look for parts of the code that are likely to have mistakes. All the problems are fixed, or at least understood and double-checked.
Some code, such as digital filters, graphical user interfaces and inertial navigation systems, are so well-understood that software tools have been developed to write the software. In these cases, specifications are developed and reliable software is produced automatically.
Unit testing
“Unit test” code is written to exercise every instruction of the code at least once to get 100% code coverage. A “coverage” tool is often used to verify that every instruction is executed, and then the test coverage is documented as well, for legal reasons.
This test is among the most powerful. It forces detailed review of the program logic, and detects most coding, compiler and some design errors. Some organizations write the unit tests before writing the code, using the software design as a module specification. The unit test code is executed, and all the problems are fixed.
Integration testing
As pieces of code become available, they are added to a skeleton of code, and tested in place to make sure each interface works. Usually the built-in-tests of the electronics should be finished first, to begin burn-in and radio emissions tests of the electronics.
Next, the most valuable features of the software are integrated. It is very convenient for the integrators to have a way to run small selected pieces of code, perhaps from a simple menu system.
Some program managers try to arrange this integration process so that after some minimal level of function is achieved, the system becomes deliverable at any following date, with increasing amounts of features as time passes.
Black box and acceptance testing
Meanwhile, the test engineers usually begin assembling a test rig, and releasing preliminary tests for use by the software engineers. At some point, the tests cover all of the functions of the engineering specification. At this point, testing of the entire avionic unit begins. The object of the acceptance testing is to prove that the unit is safe and reliable in operation.
The first test of the software, and one of the most difficult to meet in a tight schedule, is a realistic test of the unit’s radio emissions. This usually must be started early in the project to assure that there is time to make any necessary changes to the design of the electronics.
Certification
Each step produces a deliverable, either a document, code, or a test report. When the software passes all of its tests (or enough to be sold safely), these are bound into a certification report, that can literally have thousands of pages. The designated engineering representative, who has been striving for completion, then decides if the result is acceptable. If it is, he signs it, and the avionic software is certified.
At this point, the software is usually very good software by any measurement.
Monday, May 4, 2009
Garmin Aviation GPS
120-Day JA Air Center Warranty!
The GPSMAP 296 builds on the tradition of Garmin aviation handhelds like the GPSMAP 196 and GPSMAP 295. New features like terrain cautions and alerts, sectional chart-like topographic data, a built-in obstacle database of the U.S., and a transparent navigation arc view for course, speed, and distance information lead the list of advances. The GPSMAP 296 also features USB data transfer, faster processing speed, and a rechargeable lithium-ion battery pack. Press a button, and you have your choice of the unit's automotive or marine modes.
Garmin delivers terrain awareness in an intuitive Terrain mode on the GPSMAP 296. The unit combines GPS position, GPS altitude and topographical mapping to give pilots a vivid depiction of potential terrain hazards.
Pilots gain terrain awareness in a number of ways:
Terrain and obstacle information
By using visual cues and tone alerts, pilots can be aware of potentially dangerous terrain or obstacle conflicts along the current flight path. The unit also offers a configurable look-ahead warning function which gives the pilot additional time to make critical decisions.
Configurable buffer zones
The pilot can set the minimum limits to receive terrain cautions. The unit then presents potential hazards in yellow (to indicate ground proximity of 500-1000 feet) and red (to indicate ground proximity of 100 feet or less).
Obstacles database
Users can view the elevation or relative altitude of any obstacle (towers, buildings, etc.) within the unit’s built-in database. (This feature is only available with the Americas version.)
Terrain proximity cautions and alerts pop up as digital thumbnail images in the lower left-hand corner of any page whenever a potential hazard conflict looms ahead.
Sunday, May 3, 2009
Where to find Avionics parts?
Finding and locating avionics for aircrafts is a very time consuming operation as this field is very complicated and contains piles of parts in every machine. In addition to this, different types of aircrafts use different types of avionics which are manufactured by different companies. Wbparts is the only place that gathered all of these avionics in one place.
Wbparts had compiled a huge database that contains over 13 million aircraft parts including avionics. Wbparts has a wide spreading global network of suppliers all over the world, they are able to procure any type of aircraft parts including avionics in the least time ad with the best price.
When you enter their website you will be able to locate the avionics part that you need through the NSN part search. This is the most efficient way to locate an aircraft part. The NSN part search or the national search number part search is the standard way to identify an aircraft part including avionics.
All the parts in the inventory are arranged through the NSN part search criteria. In this way even if you do not know the specific NSN number of the part you can drill it down via our advanced search options.
If you are looking for avionics for an aircraft then you are in the right place. Just use the NSN part search and identify the avionics you need then request a free quote. After that you will receive the part anywhere in the world.
Panasonic Avionics Corporation Selected by Air France - KLM to Provide World Class Entertainment on Air France’s New B777-300ER
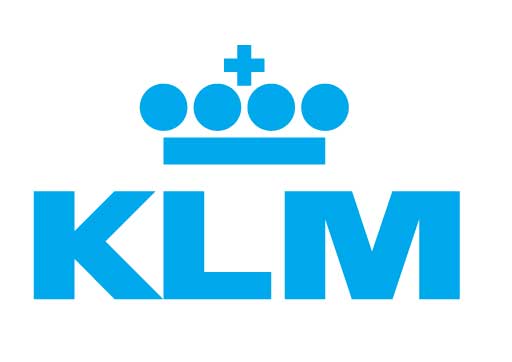
“Since early 2008, we have been operating Panasonic’s eX2 on our KLM B777s. We are now pleased to enter into an agreement with Panasonic to install eX2 on Air France’s B777-300ERs. The combination of our IFE programming recently recognised by the aviation industry’s 2008 WAEA Avion award, and Panasonic’s leading eX2 system, will allow Air France to provide the best entertainment to its clients. The Panasonic eX2 system was chosen for its reliability, space-saving and weight reduction which will truly improve our aircraft fuel efficiency. It is also Air France – KLM Group’s intention to leverage the synergy of Panasonic eX2 currently operating on KLM B777-300ERs,” said Patrick Roux, SVP of Marketing, Air France - KLM.
“This is a proud moment for us to be chosen by Air France - KLM,” said Yasu Enokido, President of Panasonic Avionics Corporation. “We are excited to contribute to their success and to continue our longstanding relationship with Air France - KLM.”
Panasonic develops and manages in-cabin content and services that help airlines attract passengers and differentiate their brands. Panasonic’s product suite of in-flight entertainment systems includes eX2, eFX, eXpress, and Digital MPES. eX2 features a powerful network, high-speed communication tools, state-ofthe-art entertainment content and award-winning peripheral devices.
With more than 900 in-flight entertainment systems ordered and delivered to airline customers worldwide, Panasonic eX2 is the world’s best-selling, long-haul premium entertainment option for airlines.
About Panasonic Avionics Corporation
Panasonic Avionics Corporation is the world’s leading supplier of in-flight entertainment and communication systems. The company’s best-in-class solutions, supported by professional maintenance services, fully integrates with the cabin enabling airlines to deliver the ultimate travel experiences with a rich variety of entertainment choices, resulting in improved quality communication systems and solutions, reduced time-to-market and lower overall costs.
Established in 1979, Panasonic Avionics serves over 200 customers worldwide and provides systems on over 3,700 aircraft. Headquartered in Lake Forest, California, the company employs over 2,600 employees with operations in 80 locations worldwide. For additional information, please visit www.panasonic.aero
Panasonic Avionics Corporation is a subsidiary of Panasonic Corporation of North America, the principal North American subsidiary of Matsushita Electric Industrial Co., Ltd. (NYSE: MC). Additional information on Matsushita Electric and Panasonic is available at www.panasonic.com
Saturday, April 25, 2009
Avionics of F-22
The F-22's advanced integrated avionics suite allows the pilot to operate in battle conditions without the burden of managing individual sensors, thereby dramatically improving situational awareness and improving the performance of the pilot and aircraft. "Release of the Block 3.1 software is a significant enhancement to the war fighting capabilities already demonstrated by the Raptor," said Bob Rearden, Lockheed Martin F-22 vice president and general manager.
F-22 Raptor prime contractor Lockheed Martin Aeronautics Co. is principally responsible for the successful development and initial testing of the aircraft's advanced integrated avionics suite at both its Marietta, Ga., and Fort Worth, Texas, facilities. F-22 team partner Boeing is responsible for final integration, testing and software delivery for the F-22's advanced avionics.
"Block 3.1 supplies more than 90 percent of the total functionality planned for the F-22, and allows the flight-test program to accomplish its objectives," said Bob Barnes, Boeing vice president and F-22 program manager. "The team is very encouraged by the initial dynamic testing of Block 3.1 in our airborne and ground-based labs."
Prior to delivery, Boeing rigorously tested the software at the company's Avionics Integration Lab and on its 757 Flying Test Bed, both located in Seattle, Wash.
The avionics lab and flying test bed are helping reduce avionics risks and contain development costs by enabling extensive evaluation and troubleshooting before full avionics are installed on the F-22. To date, more than 98 percent of the avionics system anomalies have been found prior to delivery to the F-22 due to the team's extensive experience in large-scale integration, high-fidelity facilities, tools and processes. The team has been testing the Raptor's avionics packages at both the lab, since 1998, and on the flying test bed since March 1999.
History of Avionics
The term avionics was not in general use until the early 1970s. Up to this point instruments, radios, radar, fuel systems, engine controls and radio navigation aids had formed individual (and often mechanical) systems.
In the 1970s, avionics was born, driven by military need rather than civil airliner development. Military aircraft had become flying sensor platforms, and making large amounts of electronic equipment work together had become the new challenge. Today, avionics as used in military aircraft almost always forms the biggest part of any development budget. Aircraft like the F-15E and the now retired F-14 have roughly 80 percent of their budget spent on avionics. Most modern helicopters now have budget splits of 60/40 in favour of avionics. (F-22?)
The civilian market has also seen a growth in cost of avionics. Flight control systems (fly-by-wire) and new navigation needs brought on by tighter airspaces, have pushed up development costs. The major change has been the recent boom in consumer flying. As more people begin to use planes as their primary method of transportation, more elaborate methods of controlling aircraft safely in these high restrictive airspaces have been invented. With the continued refinement of precision miniature aerospace bearing, guidance and navigation systems of aircrafts have become more exact.